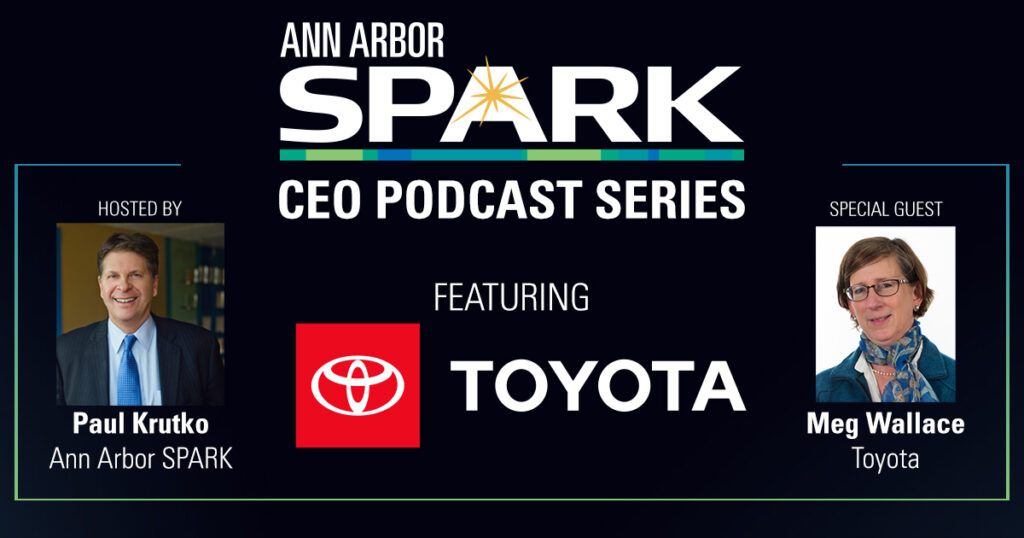
In this episode, Paul interviews Meg Wallace, Senior Engineer at Toyota North America, discussing various initiatives aimed at workforce development and educational outreach in the automotive industry. They delve into Toyota’s efforts to start the Michigan FAME Mitten Chapter, a work-study program for advanced manufacturing technician training, and Toyota’s “Driving Possibilities” initiative, focusing on K-12 STEM education and career readiness. The conversation touches on Toyota’s local presence, investment, and adaptation to the evolving mobility sector.
READ INTERVIEW
Paul Krutko: Welcome to the Ann Arbor SPARK CEO Podcast, conversations on economic opportunity. My name is Paul Krutko and I’m the president and CEO of Ann Arbor SPARK. Joining me today is Meg Wallace, senior engineer at Toyota North America. Meg is a graduate of Georgia Tech and started her career at Toyota research development, working in seat evaluation and development.
Meg’s role focuses on workforce development and she recently led Toyota’s efforts to start the first chapter of FAME, the Federation for Advanced Manufacturing Education in Michigan, which is called the Michigan FAME Mitten Chapter.
Meg has also been a part of the leadership team for Toyota’s new K through 12 STEM and Career Readiness Initiative, Driving Possibilities, which will focus on the Lincoln Consolidated and Ypsilanti Community schools.
Thanks for taking time out of your busy schedule to talk with us today, Meg.
Meg Wallace: Thanks so much for inviting me to talk about some of Toyota’s initiatives. It’s really an honor.
Paul: Well, cool. Toyota has been a great partner for us for the entire time of SPARK’s existence—we’re almost into a third decade, so it has been almost 20 years. So we’re really pleased to talk about what’s going on in Toyota because of that relationship.
So Michigan has, obviously when we’re talking about Toyota, a rich history in the automotive industry. How has the talent pool in our region contributed to Toyota’s R&D efforts and what steps has the company taken to attract and retain top talent?
Meg: So of course, Southeast Michigan is the epicenter of the automotive industry and has such a rich pool of talent already. But one of Toyota’s core philosophies, as you know, is continuous improvement. So we’re always looking for ways to do better. And that’s why we wanted to bring the FAME Advanced Manufacturing Technician Training Program to Michigan. FAME is an employer-led collaborative. It’s a work-study program that was created by one of Toyota’s brilliant technicians at our plant in Kentucky about 15 years ago, and is now spreading around the country under the auspices of the Manufacturing Institute. As you well know, Melissa Sheldon at Ann Arbor SPARK and the folks at Washtenaw Community College have been really instrumental in getting the Michigan FAME chapter, the mitten chapter off the ground. The FAME Mitten chapter is one of the key initiatives we’ve taken to attract and develop the next generation of talent in Michigan.
The other major initiative of ours is Driving Possibilities, which will focus more on the K through 12 space in order to get students in our area to be more interested in STEM and ready for STEM careers.
Paul: Well, I appreciate that. Also, you might want to talk a little more in-depth on that. FAME is focused on beginning to develop, I guess I would say, an increasing cadre of advanced manufacturer technicians. What is an advanced manufacturing technician in general? I know it’s probably a lot of specifics, but can you describe that a little more?
Meg: Yeah, so an advanced manufacturing technician is sort of like a technician who maintains the equipment at a plant, and is a very in-demand career. And, you know, in order to do that job, you need sort of a technical background, as well as, to be a global best advanced manufacturing technician, it’s good to know about professional behaviors, know about manufacturing, core learnings. And yeah, so it’s a field that is always looking for more people. And so FAME is a great way to sort of funnel students, make students more aware of that career opportunity, and to funnel students into that career opportunity.
Paul: Yeah, someone explained it to me in terms of another project we’re working on, which is to get the designation from the federal government as a Tech Hub, that raising the skill level and expertise from the bottom up is really important because that way, you can solve problems on the shop floor. Rather than having an engineer come from someplace else down to solve that, you’re beginning to solve those problems and deal with issues right at the source. Is that a fair way to describe it?
Meg: That is a great way to describe it. And I would say that problem-solving is a key component of the FAME curriculum. The FAME curriculum has five different manufacturing core exercises that are all based on some core principles of the Toyota production system. And one of those is problem-solving. So the students will learn the Toyota problem-solving method that has been very successful.
Paul: I’m a little off-script here, but the five components, do you have those off the top of your head?
Meg: Yeah, so safety culture, visual workplace organization, lean manufacturing, problem-solving, and machine reliability are the five manufacturing core exercises.
Paul: Okay. Let’s talk a little about the initiative Driving Possibilities. It’s important for us, and I think it’s important for you that, as a company, we’re focused on certain populations who may not have had opportunities in the past. And I see by the school districts that you’re focusing on, you are emphasizing Eastern Washtenaw County, which is where we know those kinds of populations and students exist. So talk a little bit more about the Driving Possibilities program.
Meg: Right. So, yeah, it’s Driving Possibilities, something we’re really, really excited about. Driving Possibilities is actually a national K through 12 STEM and career readiness initiative that Toyota is rolling out in 14 different communities where we have operations, including here in Michigan where we have our R&D headquarters.
Here in Michigan, the Toyota USA Foundation is granting nearly $10 million over the next five years in Southeast Michigan for this initiative. So the work that we’re doing will take place in the Ypsilanti Community Schools and the Lincoln Consolidated Schools. We have very strong support from Washtenaw Intermediate School District. The work will be coordinated by a new community-focused STEM Institute led by Eastern Michigan University’s College of Education. And the Institute will be governed by the school partners and Toyota.
So the STEM Institute will provide support services, curriculum and activities to integrate STEM—which is of course is science, technology, engineering, and math—into daily experiences of students and families. So we want to create more awareness and excitement for STEM opportunities through classroom curriculum, industry field trips, speakers, camps, and exploration of career technical education.
Paul: Yeah, that’s really important because one of the things that we’ve noticed in our talent work is that sometimes, parents kind of direct their children in a certain way that manufacturing or advanced manufacturing is not the place, the career they want their child to have. And there are great opportunities there. We’ve found in some of our work that exposing the students early on to what modern manufacturing is today, can kind of overcome some of that reluctance. I mean, they’re good jobs, they pay very well, with excellent potential career ladders in them. They may be perfect for many, many students. And so I’m really excited about this initiative because it really attacks what I think is a particular area that we want to try to impact.
Meg: Yeah, I think you’re exactly right. Maybe students aren’t aware of the opportunity, or aware of how exciting and technology-focused new manufacturing careers are.
We’re having a meeting of the FAME chapter this week, and Melissa Sheldon from Ann Arbor SPARK reported that she was already hearing from one of the parents of the students at Orbitform, one of the companies who is part of the FAME chapter, saying that his son loves the new job and comes home excited every day talking about all the new things he’s learning. And yeah, I think a hands-on type engineering job like an advanced manufacturing technician job is really exciting and a lot of people are not aware of it.
Paul: Well, maybe what I’ll do is encourage my team to have a podcast episode with that student. That might be a very interesting dialogue, because you know, oftentimes it’s at the level that you and I are at, as I said at the beginning of the opening, leaders in economic development, but I think that would be very interesting to have a student that’s engaged in the FAME program on, and spend some time with them to have them be almost an ambassador for others to join the initiative.
Meg: That’s a great idea. I love that.
Paul: Yeah, I think we’ll do that. Well, let me switch gears a little bit. You know, we work closely with Toyota and we were really pleased to be supportive of, along with the State of Michigan, on the research facility here and Toyota North America’s investment. That’s almost $48 million in terms of a new facility for battery testing here. So tell us a little bit about that, and for our listener group, I oftentimes talk about Toyota, but lots of folks really don’t understand the scale of Toyota’s presence in Washtenaw County. So maybe take a little bit of time to talk about that and then share with us what this new project is.
Meg: Yeah. So we are super excited to be expanding our footprint in Southeast Michigan with the new battery lab. In terms of synergies, you know, our supply chain management operation is located here. And the new battery lab in Michigan will support our battery manufacturing plant in North Carolina and the development of batteries at our facility. But both of those are a few years away from opening.
So in terms of Toyota’s presence in Southeast Michigan, we’ve been here for more than 50 years. We’ve invested about $80 billion in the area. We have two locations, maybe sort of like two and a half locations, because we have a facility in Ann Arbor, a facility in Saline, and we also now have a small facility at the American Center for Mobility. So we are really embedded in the economic life here and see it as a great place to grow.
Paul: It’s something that we really tout that one of the strengths of Washtenaw County and the Ann Arbor region is sort of a variety of R&D facilities. And I think one of the first of scale was Toyota. But I do laugh, and I’ll share this with the audience: I’ve had the opportunity several times to come out when we have a new governor—and I’ve now been my third governor—and they want to come and visit the facility because they know the scale. And your leadership is always proud to show a slide at the beginning of Toyota’s initial presence in Ann Arbor, which was 50 years ago. It was two engineers and I think it was an early Corolla at a garage, a gas station in downtown Ann Arbor. And that’s grown to thousands of engineers. And the story is that why that happened is because we had the EPA testing facility here initially. And that was the lure. But then Toyota determined that this was a great place for them to have an R&D facility. And then over the years, one of the things that I know pretty well because of Bob Young, who’s the head of procurements activity there and has been on the SPARK board for a long time, was the notion to move the whole supply chain procurement function close to the R&D facility several years ago. So that was another growth aspect for sure.
Meg: Yes, that’s been a huge benefit to us to have our purchasing supplier development, design engineers, evaluation engineers, all co-located because it just makes development more speedy and it just makes it easier for everybody to see the development process.
Paul: So maybe some broad questions as we kind of finish up on the podcast today. The mobility sector is really seeing significant transformations in recent years. How is Toyota North America adapting to these changes and aligning its R&D strategies to meet the evolving needs of consumers?
Meg: Yeah, so, it’s a huge time of change in our industry and Toyota believes wholeheartedly that electric vehicles are the future. But we have to look at the organization as a whole, and talent development as a whole, for the whole organization. And so we’re looking to curate future talent through programs like Driving Possibilities and to support the immediate needs of our talent pool through programs such as FAME.
I think that we’ll be, you know, through Driving Possibilities, we’ll be trying to encourage CTE program and through the Ypsilanti and Lincoln schools the career technical education, that will have more of a focus on future technology and will be informed by industry needs.
And similarly, the whole premise of FAME is that industry is partnering with local community colleges to make sure that what students are learning at school meets the needs and future direction of employers. Both FAME and Driving Possibilities will support the EV future in Michigan by supporting students to become STEM problem-solvers.
Paul: Very good, very good. Yeah, so we’re really pleased also, and you already alluded to it, that Toyota has taken advantage of the facility at the American Center for Mobility, as many other companies have because it is an open-source environment. But as you said, Toyota has actually developed a building on the site and has a group of engineers working very hard not only on electric vehicles, mainly they’re working on connected and autonomous vehicle work there. And so it’s been, just the growth of engagement with the company has just been really important for the region’s economic growth over the last decade.
So it’s always good to check in as we’re doing today and have a conversation about what’s going on. And we’re really excited that Toyota looked to SPARK to be a partner on the FAME initiative. It’s something that we’re really pleased to be involved in.
Meg: Well, we have certainly appreciated your help. It’s been invaluable. So really excited for that partnership and to see how FAME develops and perhaps spreads to other areas.
Paul: Yeah. And really what I also think is important about it is Toyota is sort of in a giving back way demonstrating what other companies could do as well. So one of the things that’s always great when a private sector partner does what you’re doing with those two programs, is you’re kind of showing others what they should be involved in as well. So we appreciate that leadership as well.
Meg: That’s a great point. And we are hoping that other companies will get involved. I mean, of course, FAME is a collaborative of companies, but Driving Possibilities, we’re also hoping other companies will get involved with it.
Paul: Yeah, I think it’s really, really important. And one of the things that I alluded to that we’re working on is this large federal request that is a national competition. It’s not like it’s a given that we’re going to get it, but we want to highlight the fact that we would be investing in more programs like Driving Possibilities, because as you know, and we didn’t really touch on this in the conversation, the shift from internal combustion engines to EVs or hybrids, as I know, there needs to be a transition. We can’t just go straight from ICE to EVs because of a variety of reasons. But we need to rework and train not only the young folks coming up, but people that are in the industry now because it’s a different kind of manufacturing and it’s a different vehicle platform. And so that whole concept, I think both the federal government, the state government, we as a regional public-private partnership, we want to make sure that all the people that live in our region have those opportunities. And I think that’s what’s great about these programs. We want them to be able to transition as the mobility industry is transitioning. We need the workforce to transition as well.
Meg: Right. That’s a great point.
Paul: Well, great, Meg. I want to thank you for taking some time to talk with us today about the exciting work that you’re involved in at Toyota and what Toyota is doing here in the region.
Meg: Thank you so much. I’ve really enjoyed talking to you.
Paul: And I want to thank our audience for listening and learning more about those leaders and organizations working hard to create the Ann Arbor Region’s economic future. These conversations are brought to you by Ann Arbor SPARK. For more information about Ann Arbor SPARK, you could find us on the web at annarborusa.org and also on Facebook, Instagram, and LinkedIn.
Meg Wallace’s Bio
Meg Wallace works for Toyota Research and Development in Saline with a focus on Workforce Development. Recently, Meg has led Toyota’s efforts to start the first Chapter of FAME (Federation for Advanced Manufacturing Education) in Michigan, which is called the “Michigan FAME – Mitten Chapter.” Meg has also been part of the leadership team for Toyota’s new K-12 STEM and career readiness initiative, Driving Possibilities which will focus on the Lincoln Consolidated and Ypsilanti Community Schools.
Meg has a degree in Mechanical Engineering from Georgia Tech and worked in seat development at Toyota on such vehicles as the Sienna and Avalon.
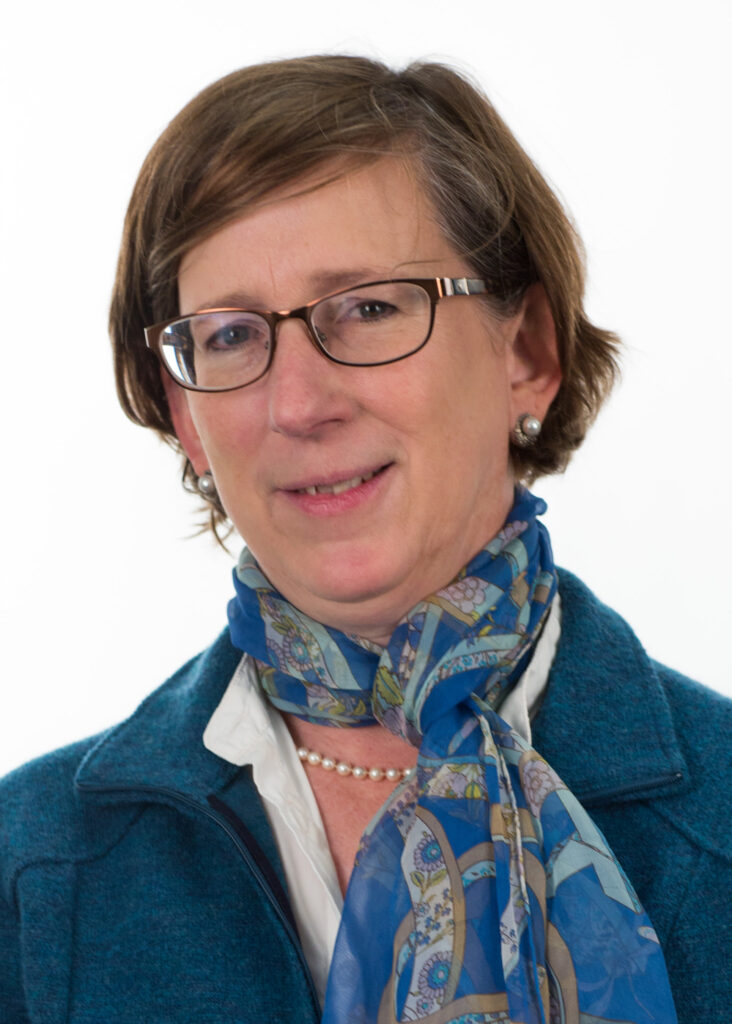